You've come to the right spot because today I'm going to show you how easy it is to cut a re-usable vinyl stencil with your Silhouette to make screen print shirts with a silk screen.
I previously shared a tutorial on Silhouette School Blog about how to make your own silk screen hoop for screen printing. But for this tutorial I am going to introduce you to the Speedball Silhouette Screen Printing kit. The kit comes with everything you need to screen print aside from the shirt! (Tip: Mix the included paint colors to make more!)
The vinyl included in the kit is 651/permanent outdoor vinyl which is perfect for making vinyl screen printing stencils that can be used about 5 or 6 times before the vinyl starts to get a little wonky.
The first thing you want to do is find a design or create one in Silhouette Studio to cut. Adjust your settings for vinyl and cut the design with your Silhouette machine. If possible, position the design so it cuts in an area of the vinyl where you will have a decent size vinyl border - at least an inch or two on each side.
When you weed the vinyl stencil design, you want to weed out or remove the vinyl from the area that you want to paint. Leave the vinyl in the area where you want the shirt to show through.
Cut off a piece of transfer tape that's big enough to cover the entire design. Place the transfer tape over the entire vinyl design and use it to move the vinyl stencil into the center of the screen.
You'll want to place the vinyl on the side of the screen where "Speedball" is facing up on the frame and the screen is basically touching the table. Remove the transfer tape, leaving the vinyl behind on the silk screen.
Grab some painters tape (1.5" - 2" works best) and tape around all four edges of the vinyl design. This will prevent any paint from getting through the screen on areas where you do not want paint.
Lay your shirt on a flat, firm surface and make sure there are no wrinkles. Slide a piece of cardboard into the shirt to protect the opposite side from any paint that might otherwise bleed through from front to back.
Place the screen on top, positioning the vinyl stencil exactly where you want it.
Using a foam brush, blot a thick line of Speedball Fabric Ink along the top edge of the vinyl (or covering the design). Then in a swift downward motion, use the squeegie to firmly and swiftly scrape the paint across the screen and design so it seeps through the screen and onto the shirt. Repeat with one more download swipe if necessary.
Pull up the screen to reveal your beautiful screen print!
After the paint has dried, apply heat (between 320 and 325 degrees) with an iron or heat press to cure the paint so it doesn't bleed when it sets and becomes permanent.
The vinyl screen print stencil can typically be used about 5 times before the vinyl starts to lift. The screen can be washed with water and mild soap.
Isn't that awesome?! I am totally loving the results and am actually amazed at just how crisp and sharp the paint lines are. Want to try it too? You can grab a vinyl screenprinting kit here.
Note: This post may contain affiliate links. By clicking on them and purchasing products through my links, I receive a small commission. That's what helps fund Silhouette School so I can keep buying new Silhouette-related products to show you how to get the most out of your machine!
Thanks for coming to class today at Silhouette School. If you like what you see, I'd love for you to pin it!
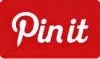
Get Silhouette School lessons delivered to your email inbox! Select Once Daily or Weekly.
We have been using heat transfer vinyl, and our Silhouette Cameo, to make shirts for our friend's business. Not a huge amount of shirts, but the design is a bit difficult to weed, and each shirt uses 12" X 12" of heat transfer.
ReplyDeleteI looked at this post and your post about using an embroidery hoop to make a silk screen. Then I checked the internet to find out about making a silk screen frame.
In theory, I can combine the great information you posted, make a largish silk screen, and then heat transfer the vinyl to the silk screen. This would make a permanent reusable silk screen, and drive down the cost and the time needed to make the shirts.
And I would have to think about whether to put the vinyl on the side of the screen that contacts the shirts, and there would be no ink creep, or it does not matter, because your screen prints look very sharp.
Thank you for another of your great posts, and this one was even more thought provoking than usual.
That's exactly what I was thinking after reading this. HTV would be a more permanent solution.
DeleteThis comment has been removed by a blog administrator.
ReplyDeleteWhen you use your heat press at 320 or 325 how long do you heat your shirt?
ReplyDeleteAbout 20 seconds
DeleteThis comment has been removed by a blog administrator.
ReplyDeleteThis comment has been removed by the author.
ReplyDeleteThis comment has been removed by a blog administrator.
ReplyDeleteThis screen printing step by step methods sounds to have great value and this vinyl type print has unique feature in it
ReplyDeleteThis is a great tutorial! Can you use the screen more than once for a different design?
ReplyDeleteYes you can use it several times before the vinyl starts to peel up
DeleteHow does the ink feel after it dries? I used fabric paint before, and it was very stiff. Is this going to feel stiff also?
ReplyDeleteWhat does the fabric feel like after the paint has dried? Is it stiff?
ReplyDeleteIt is slightly stiffer than the shirt area that does not have the transfer
DeleteI really like using textile ink instead of paint. It looks much more professional and feels better on the fabric. Most inks need to be heat cured. However, Aerotex ink from Union Ink cures without heat. There is a catalyst you mix into the ink before you use it. That is what does the curing. I really like that ink.
ReplyDeleteI just bought the new cameo 3 with the screen printing kit, hopefully it will be here this week I cant wait!
ReplyDeleteVery informative. Can we use anything else in the place of vinyl for screen printing
ReplyDeleteThis is a wonderful idea. Thank you so much for the tutorial!! Love all you instructions.
ReplyDeleteCan a screen be used to make stencils for on wood instead of fabric? I read the comment about using HTV on the silk instead of Oracal 651. Love that idea. I'm wanting to make a silk stencil that I can use to make several identical wood signs. Any suggestions?
ReplyDeleteThanks
I know this was posted a little while ago, but I have some questions I'm hoping you can answer! I have a Cricut and have been using Cricut brand regular vinyl, not heat transfer. I weed it out and put the transfer tape on. I stopped using Cricut brand transfer tape because it was way too strong :( someone told me to get contact paper from Walmart so I got that instead. However, it has been taking me so long to get it on the screen because first all my pieces (like the insides of the O's or P's, etc) will be difficult to get onto my transfer tape. Then once I finally get it on the transfer tape, it'll take just as long getting it all to stick to screen. And in top of that I always end up with bubbles despite being very careful. We've done 5 or 6 shirts and I feel like I'm wasting money :/
ReplyDeleteShould I be using a different vinyl or transfer tape? Maybe silhouette brand? I really want to start up a business but there's no way when it takes me 2hours for one simple shirt :(
Thank you in advance!
Great tutorial... I have the Speedball kit, and have tried 3 times now to get my 651 stencil to stick to the screen, and it just refuses to adhear. Any suggestions?
ReplyDeleteI am having this exact problem!
DeleteI am doing this from start to finish with my boys. Thank you SO much for laying it out so nicely. identification card
ReplyDelete